We live in a world of fast or disposable fashion. This industry is increasingly impacting the environment due to the use of toxic chemicals, water and energy consumption, heavy transportation and do not get me started on textile waste. Put mildly, the current fashion industry isn’t very efficient. It’s time we start to do things differently. We wonder, how can we (re)introduce biology to design a less harmful future of fashion?
From animal skin to synthetic skin
Wearing clothes is an exclusively human characteristic. As our ancestors migrated to colder climates, they used animal skins and vegetation to protect themselves from the weather. One can only thank our genius ancestors for coming up with the brilliant idea of using an animal skin as a coat!
Over time, we’ve grown accustomed to using clothing as an extension of our skin, and traditional materials like leather, silk, cotton and wool (all products of nature) became the norm for the fabrics that we wear from day-to-day.
Yet over the course of the 20th century we have replaced those natural materials for their synthetic counterparts (such as nylon and polyester— because they are easier to produce and can be engineered with more precision). These synthetic materials came with the price of pollution and waste: Our current fashion industry is responsible for ten percent of all CO2 emissions.
Promisingly, a new wave of designers has arisen to tackle these issues by making smart use of biology. Combining biology and design, we are now able to create products that adapt, grow, sense and repair themselves. We took a plunge into the most innovative designers that are radically stirring the fashion industry by cultivating new (forms of) textiles.
Six fashion designers from the future
Imagine you could grow your own clothes using fermented tea, bacteria, yeast, and other microorganisms that can spin the ingredients into eco-friendly fibers. This is exactly what fashion designer Suzanne Lee pioneered: Biocouture.
Lee has been utilizing bacteria in a vat of liquid to produce bacterial cellulose. Cellulose is a useful organic compound that also appears in for example wood and cotton - but these are less sustainable than its bacterial counterpart.
From the leather-like material Lee developed a range of prototypes, but her goal goes beyond the production of individual pieces. Back in 2015 she told us “lab-grown materials will have real impact on the fashion and textile industry.” Eventually, the material should be alive while we wear it, nourishing and protecting our body. Currently, Lee is working at Modern Meadow on a collagen based bioleather called Zoa.
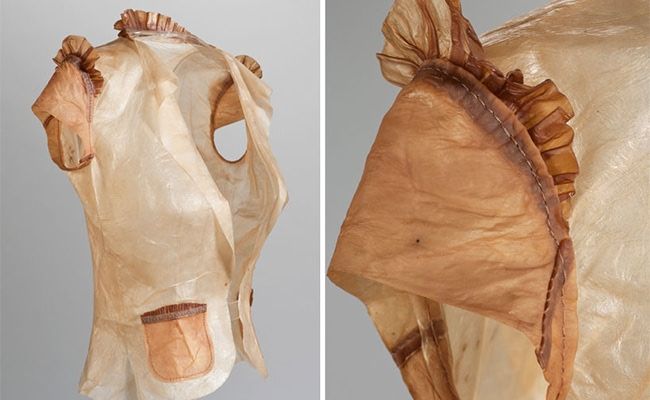
In the same line of thought, designer Roya Aghighi developed the project Biogarmentry in collaboration with the University of British Columbia. The project pursuits to create a biodegradable living textile that is capable of photosynthesis. The first proof of concept is a 100% natural and biodegradable textile that purifies the air.
In contrast to synthetic clothing that does not require much human attention, biogarmentry has to be taken care of like a plant. One argues it challenges our relationship to the clothing we wear everyday and it encourages us to develop a long lasting - perhaps even intimate - relation with the things we wear.
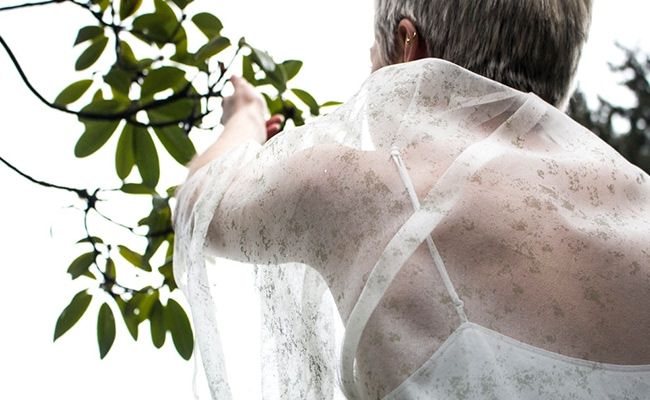
Seaweed is another natural material that has promising characteristics. Focusing on circularity and ecological health, the company AlgiKnit is creating rapidly degradable yet durable yarns derived from a seaweed called kelp.
Kelp is one of the fastest growing organisms on earth, that grows in the ocean and therefore does not need any fertilizers or fresh water. Inspired by nature’s ability to self-repair and recycle, AlgiKnit creates textiles from biopolymers that can, when worn out, serve as nutrients for the next generation of AlgiKnit’s materials.
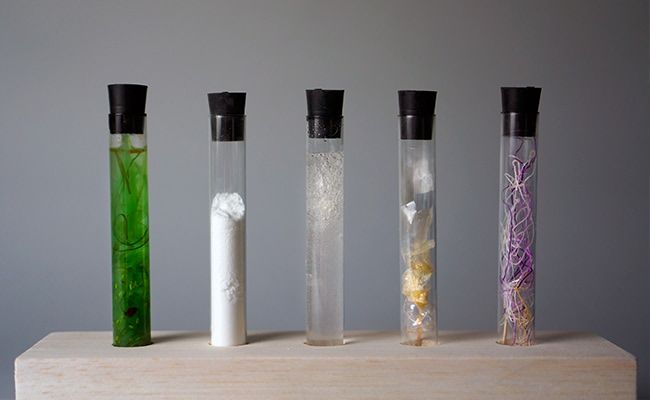
Quite similar to seaweed, Tjeerd Veenhoven explores the qualities of algae. Algae are fast-growing and globally available from oceans and lakes. Their natural growth is a crucial element in carbon flux, as the organism converts large volumes of CO2 to oxygen. Veenhoven’s project AlgaeFabrics develops a strategy on how to create a sustainable textile derived from algae cellulose. Cladophora, the specific species of algae they work with, is especially effective in its cellulose production and proves to be an excellent material to make yarn from.
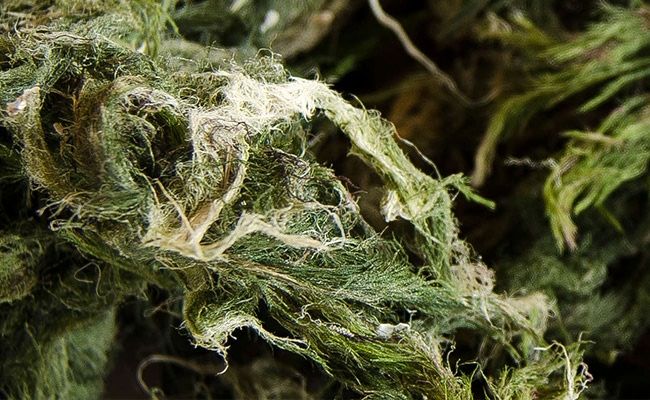
Fungi and mycelium are already regularly used to design rigid objects such as vases and furniture. Designer Aniela Hoitink developed a flexible mycelium-based material that is applicable as a textile: MycoTEX.
Instead of arguing against the fast pace by which fashion items are disposed, Hoitink considers the short life cycle of textiles an opportunity. She developed MycoTEX because it can be used explicitly for a short life cycle. Instead of changing our behavior of consumption, Hoitink proposes to change the lifespan and degradability of materials.
Growing mycelium directly into a piece of fashion using 3D modelling, she skips the steps of spinning yarns and weaving or knitting it into a cloth. This ensures effective use of the material, less industrial processing and a reduction of waste. It is 100% degradable and can be put into the ground after use.
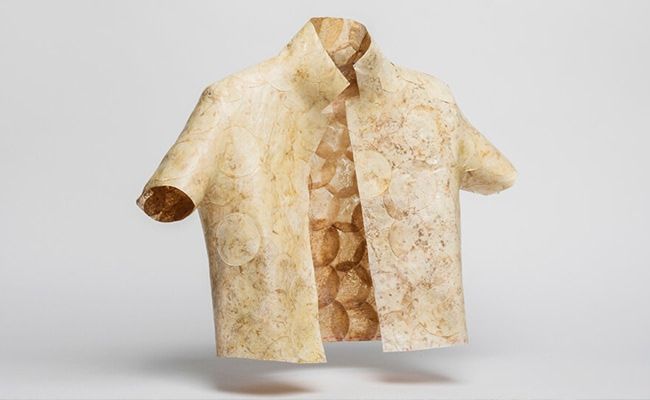
And last but not the very least, fashion needs colour! NNN members Laura Luchtman and Ilfa Siebenhaar are working on Living Colour, an ongoing biodesign project that aims to color the world in a sustainable way. They are exploring alternatives to toxic textiles dyes and have found their solution in pigment-producing bacteria. They even created colored patterns by subjecting the bacteria to different sound frequencies. Their colors can be applied to all textiles, and has also been successfully tested on Hoitink’s MycoTEX.
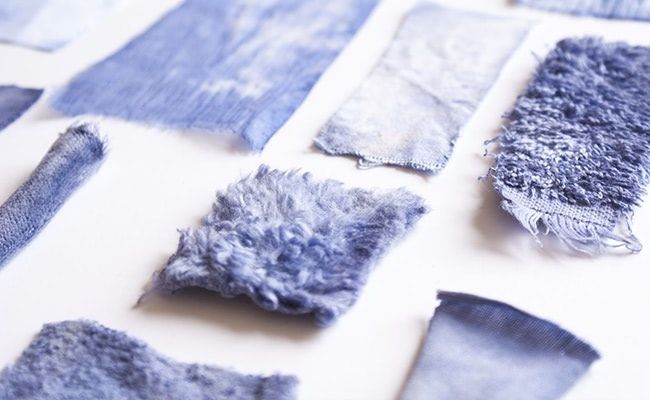
Is bio design really the future of our fashion industry? Ista Boszhard and Cecilia Raspanti, founders of Waag’s TextileLab, believe it is. Out-of-the-box experiments are necessary to challenge the status quo. Experimenting and researching biomaterials changes our relationship with textiles and challenges us to think differently about the way we produce and consume fashion. Collaboration and sharing resources - between designers and scientists of all sorts - are key to move towards a circular industry.
Not all materials are equally promising in terms of upscaling, but Boszhard wholeheartedly comments that “we shouldn’t be looking for the next plastic or the next cotton.” Instead of trying to invent a material that can be used for all types of clothing worldwide, the key is to develop and choose materials that are flourishing in the climate of the region and fit our specific needs.
Let’s celebrate the strong qualities of synthetic materials in an industry of slow fashion, and use biodegradable textiles to cater our wishes of fast fashion.
"|
Comments (0)
Share your thoughts and join the technology debate!
Be the first to comment!